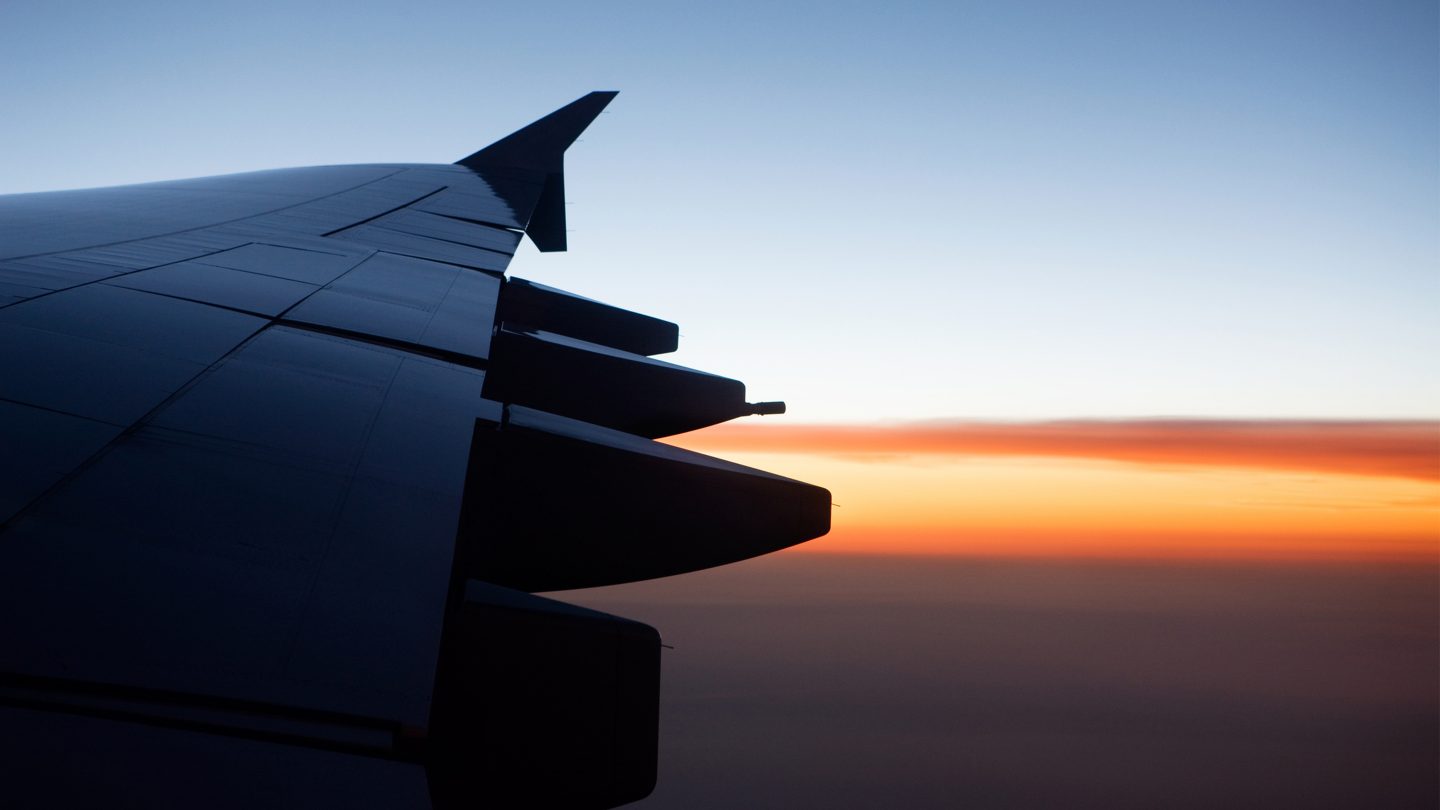
Client
Airbus
Client
Airbus
Project
Connected Factory Solutions
Industry
Aerospace
Services
Customer Experience (Cx)
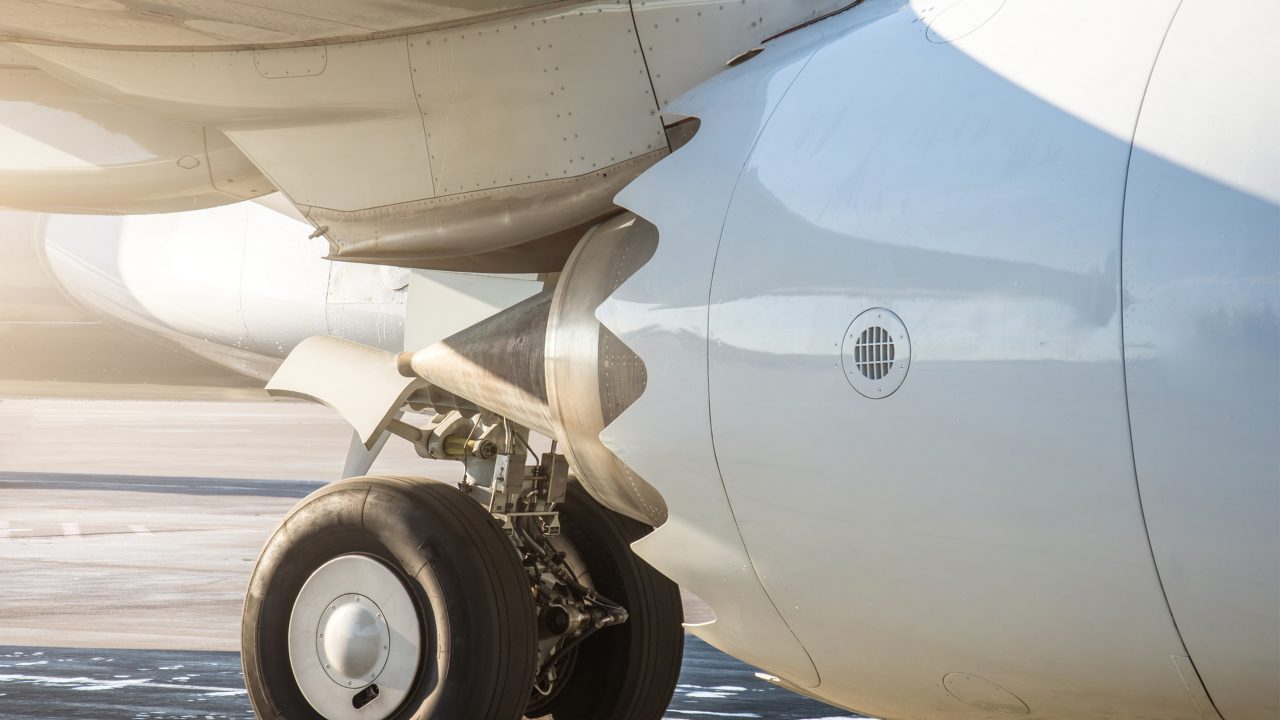
Background
As a leader in the aerospace sector, Airbus designs, manufactures, and delivers aircrafts spanning commercial aircrafts, helicopters, defense, and space.Brief
With Airbus’ goal of building the factory of the future, our team laid out a long-term strategy that would shift their business toward seamless integration of digital and physical aspects of their business.Goals
The goals for this build were to develop an end-to-end dynamic workflow management system and machine process monitoring solution to improve process efficiency and increase the effectiveness of equipment.Challenge
We had to operate with two parallel implementation tracks, one included machine connectivity & analytics solution, and the other was the implementation of a Manufacturing Execution System (MES).
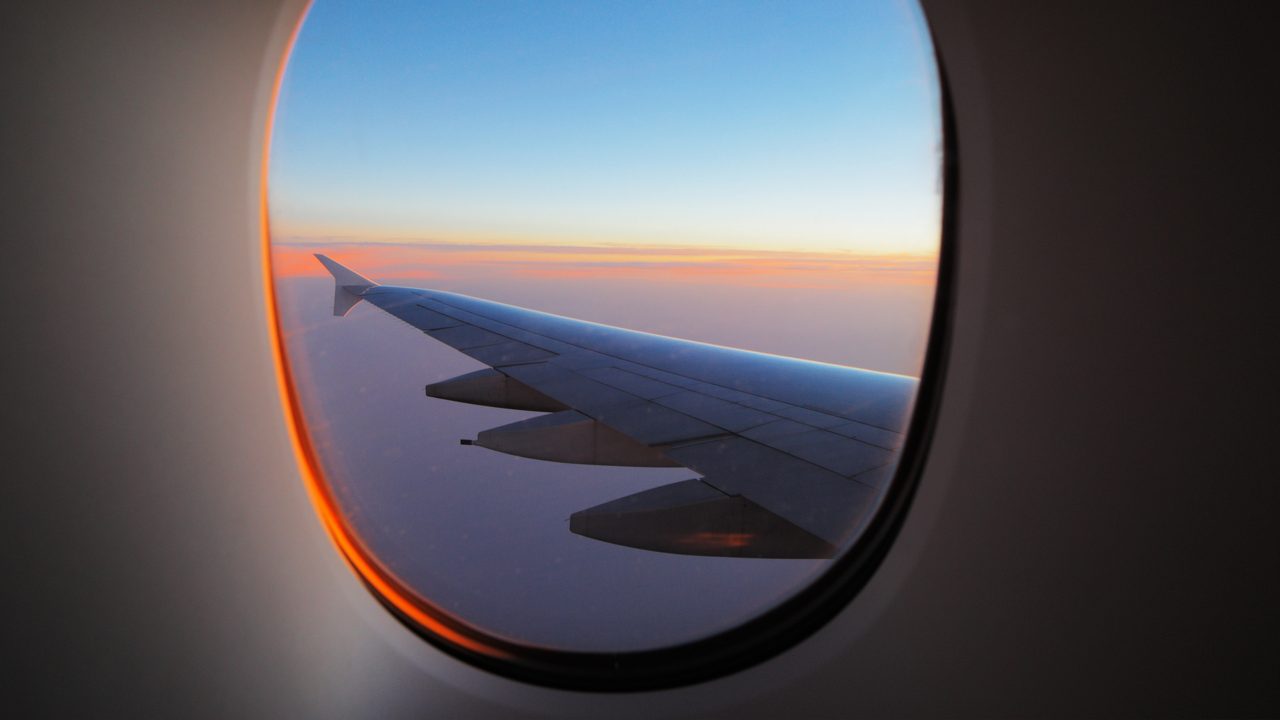
Strategic Transformation
We conducted a gap-analysis assessment to identify improvement areas and subsequently executed a Proof of Concept (PoC) to help Airbus understand the benefits and features of various solutions and advanced analytics.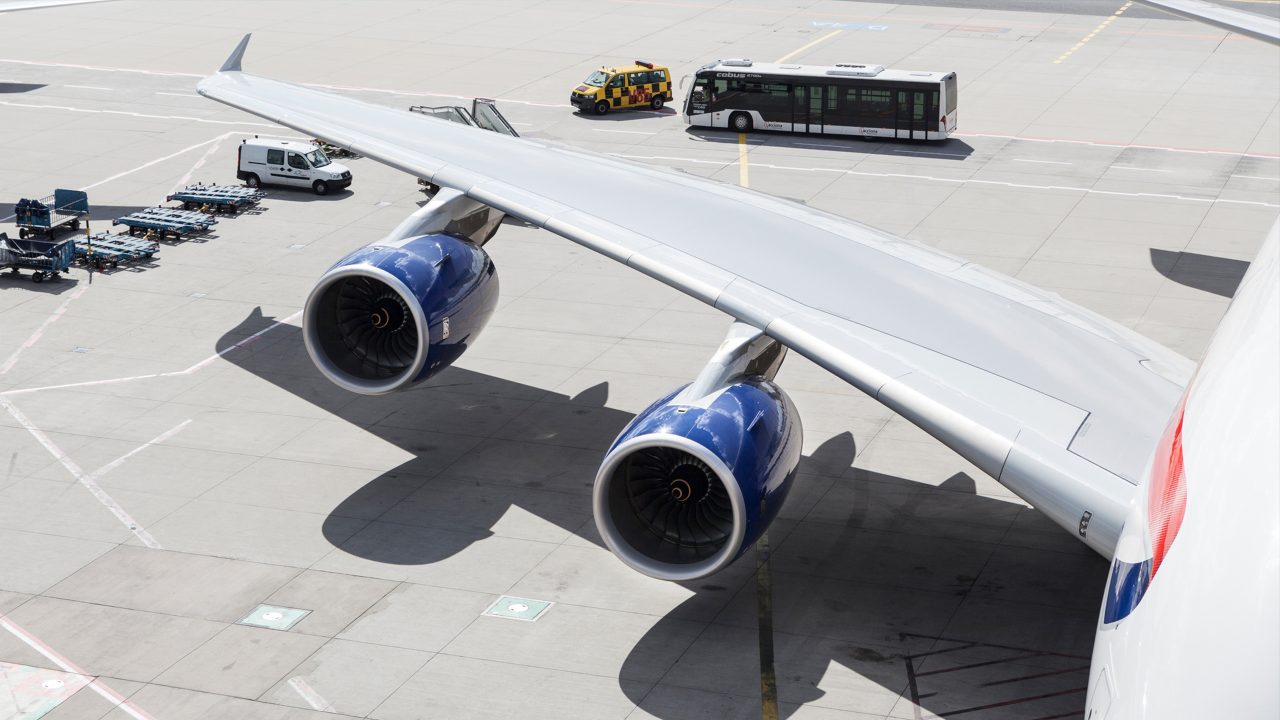